Reasons why agricultural vehicle manufacturers choose V-beam overhead cranes
V-beam overhead crane has unique advantages in the field of industrial manufacturing. As an excellent crane manufacturer, Dongqi Crane has the obligation to help customers understand the advantages and disadvantages of this overhead crane in application. Today, Dongqi Crane uses a case of installing a V-beam overhead crane in an agricultural vehicle manufacturing plant to explain the reasons why the customer finally chose this type of crane. I believe that through actual case analysis, customers can more easily understand why they should choose this crane.
Agricultural vehicle company installs V-beam overhead crane
Based in Münsterland, Germany, the company manufactures customized agricultural vehicles and distributes them to nearly 40 countries. In addition to agricultural vehicles, two workshops have recently been built on the company’s premises. Managing Director Robin Krampe said: “We need space both to build the bodies as core components of our body dump trucks and for our customer services. By constructing these new buildings we hope to achieve our ambitious goal of increasing production capacity by 25%. “
Large, heavy-duty components are welded and assembled in the first new workshop, which is used for body manufacturing and covers an area of 3,600 square meters. The task is divided between welding robots and separate workstations for manual special construction. To achieve fast throughput of up to eight vehicles per working day in the future, ergonomic considerations are key when setting up workstations.
There are also challenges in achieving a smooth flow of materials from one station to another.
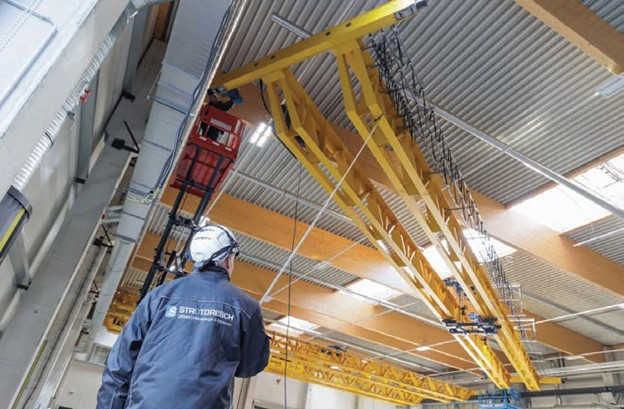
Crane Company engineers planned the entire crane system and were responsible for the crane runway and crane installation; this was a challenging task as in some cases it required the use of an external mobile crane to move the 30m long crane girder Move into the long open roof light.
Six double-girder V-type cranes with a span of 29.44m and a lifting capacity of 5.0t travel on a 90m-long shared crane runway. Up to six welded components or car bodies can be transferred simultaneously from one work step to the next and, if required, one or two workstations can be connected to each other.
Crane companies recommend V-beams as crane girders because the bionic profile design – which, similar to a skeletal structure, uses material only where necessary – enables high load capacity and low dead weight (compared to traditional box-section girders) , vibration performance increased by approximately 17%) and vibration performance improved by approximately 30%.
The second reason is that the directors of the agricultural vehicle manufacturing company worked hard to provide their employees with a well-lit working environment, allowing as much daylight as possible to reach the workplace through the 90m long roof glass. The crane company says that for the six double-girder overhead cranes, the shape of the profile makes a difference – V-shaped cranes with tapered diaphragm joints can “let plenty of light through, helping to create a safe, secure environment in new production.” Pleasant lighting atmosphere “workshop”. LED lighting provides illumination in the workshop as soon as daylight is no longer sufficient.
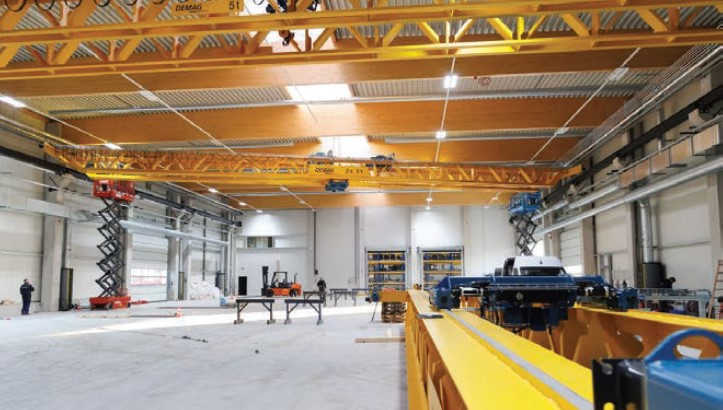
The second 800m² workshop, reserved for customer service, is equipped with a single-girder V-shaped crane with a lifting capacity of 5.0t and a span of 20.44m. Among other things, it facilitates the handling of heavy components at three service assembly stations.
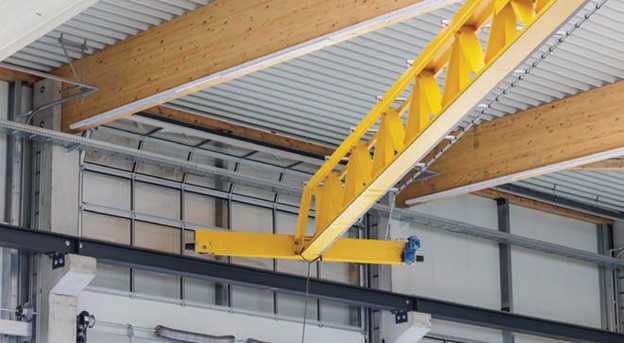
All cranes are equipped with radio control systems. Up to three transmitters can be logged per crane. For employees, this means they can change cranes at the push of a button. Therefore, operation of a single crane can be easily transferred from one employee to another. The transmitter can be replaced in seconds and unwanted activation is also prevented.
All six cranes in the larger workshop can be operated by radio in all axes (long and transverse travel, hoists) using a one-hand transmitter. The display on the controller shows the crane’s respective load capacity and operating status.
Optical anti-collision devices ensure safe crane operation and provide operators with useful convenience and assistance features. The crane electrical equipment continuously monitors and intervenes automatically once the programmed distance is exceeded. The crane stops or slows down according to the customer’s request. If operating conditions change, the distance can be reprogrammed.
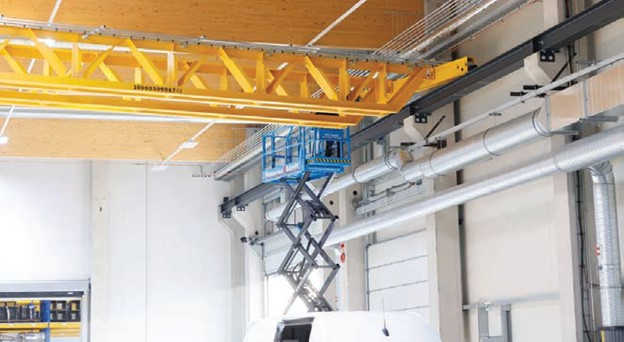
Summary of the advantages of V-beam overhead crane
Based on our work experience, our advantages of V-beam overhead cranes can be summarized as follows:
- High strength and stability: The V-beam design provides excellent strength and stability, allowing the crane to carry heavier loads. This structural form also effectively reduces the deflection and vibration of the bridge, thereby improving the operating accuracy and safety of the crane.
- Wide span: V-shaped beam bridge crane can achieve larger span and adapt to different factory and work space needs. This allows the crane to cover a wider area and improve work efficiency.
- Good rigidity and load-bearing capacity: The V-beam structure has high rigidity and can resist the effects of lateral forces and torques. This allows the crane to remain stable in complex working environments and ensure safe operation.
- Easy maintenance: The design of the V-beam overhead crane makes maintenance work relatively simple. Parts are easy to access and replace, reducing maintenance costs and time.
- Adaptable: This crane can be customized according to specific needs to adapt to different working environments and load requirements. Whether it is height, span or load capacity, it can be adjusted according to actual needs.
- Efficient and energy-saving: Modern V-beam bridge cranes usually use advanced electrical systems and control technologies to achieve efficient and energy-saving operation. This helps reduce energy consumption and running costs.
I would strongly recommend customers to use this V-beam bridge crane when they are faced with high load handling, long-span working areas, require customized solutions, have strict requirements on stability and safety, or pursue efficient and energy-saving production.