Italian cement manufacturer purchases 1 electric chain hoist for mold manufacturing plant
Dongqi Crane can provide customized lifting equipment according to customer needs. Even different factories in the same industry will have different requirements for lifting equipment. The case shared by Dongqi Crane today is that an Italian cement manufacturer customized an electric chain hoist for a mold manufacturing plant. This case will conduct a detailed analysis of the working conditions to help customers better understand how engineers can design the most appropriate crane system.
Working conditions and crane systems in mold manufacturing plants
The cement plant’s requirement was to use a hoist to lift and rotate its moulds.
These molds are used to pour cement into structures for interior design. This unusual cement is eight times stronger than concrete and its elasticity gives it the texture of wood.
However, the molds that hold liquid cement are fragile structures made of wood, rubber, resin, steel, polycarbonate and plastic. Each unique mold must be lifted and transported to a different workstation within the production facility so that the parts can be placed in the correct location to dry and the castings can be removed. An overhead mobile chain hoist is required to lift and move the moulds.
The crane company designed a twin-girder system using cable rails and mobile hoists operated by radio remote control. Technical planning of the project after preliminary analysis involved 3D modeling to verify dimensions and aesthetics, and then the sketches were approved by the client.
Engineers began working with enthusiasm and dedication, and the team built the beams and lifting clamps.
“The clamp is capable of rotating the mold 360 degrees around its center of gravity. The accessory supports telescopic molds ranging in size from 4800mm to 2800mm,” said the engineer.
The quality of the steel and welds was checked and the beams were painted. Despite the high magnitude given, the team carefully checked the actual gauge to achieve a tolerance of 1 mm.
The span of the finished suspension bridge is about 30m, and the runway is 40m long. The lifting capacity of the hoist is 5t, and the maximum lifting height is 9m.
The hoist is quiet, fast and has only 11mm sag when fully loaded as its structure is made from S355 (ex Fe510) non-alloy structural steel. The crane has proven to be very versatile and quiet, which also means we have the potential to use higher speeds.
The versatility and smoothness of the crane’s movement prevent mold breakage. “Their products are very fragile, so you have to consider not only the weight, but also the movement of the trigger and the rotation of the mold,” the engineer said.
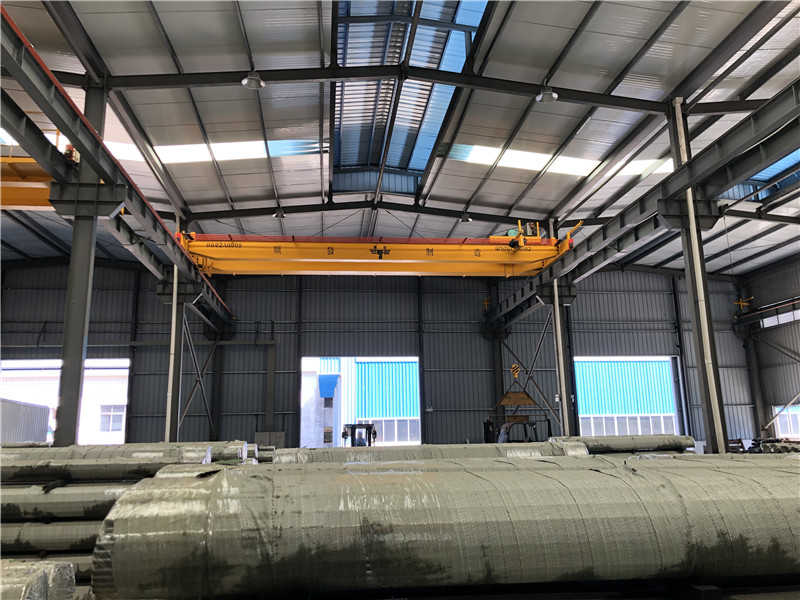
What can we learn from this
When designing a crane system for a cement manufacturer’s mold making plant, several factors need to be considered to ensure the crane’s performance, safety and longevity meet actual needs. Here are some key considerations:
Load calculation and carrying capacity:
- First, the weight, size and handling frequency of the mold must be clarified in order to accurately calculate the rated load of the crane.
- Consider the particularities of the mold, such as shape, weight distribution, etc., to ensure that the crane can meet actual operating requirements.
Structural design:
- As the main structure of the bridge, its material selection, cross-sectional size and connection method should meet the strength and stiffness requirements.
- The design of carts and trolleys should ensure smooth operation and accurate positioning, and take into account the actual conditions of track laying.
- The design of the lifting mechanism should take into account the lifting height, speed and stability of the mold.
Material selection:
- Steel is the main material of bridge cranes, and steel with high strength and good corrosion resistance should be selected.
- Consider environmental factors, such as dust and humidity in cement plants, and choose appropriate anti-corrosion measures, such as spraying anti-rust paint.
Stability and security protection:
- The stability of the crane is crucial, and the design must ensure a low center of gravity, a wide chassis, and take necessary shock-absorbing measures.
- Set limit switches, overload protection, emergency shutdown devices and other safety protection measures to ensure operational safety.
Running speed and control:
- According to the actual needs of mold handling, the operating speed of the crane is reasonably designed.
- Adopt advanced control system to achieve precise control and operation and improve operating efficiency.
Maintenance and replacement of wearing parts:
- When designing, the ease of maintenance of the equipment, such as the replacement of wearing parts and the setting of lubrication points, etc., need to be considered.
- Detailed maintenance manuals and operating guides are provided to facilitate operators to perform daily maintenance and upkeep.
Environmental protection and energy saving:
- Consider the environmental protection requirements of cement plants and choose low-noise, low-emission motors and transmission systems.
- Optimize the design to reduce the energy consumption of the crane and improve energy efficiency.
Customized design:
- According to the specific layout, operation process and space constraints of the mold factory, customized design is carried out to ensure that the crane can be smoothly integrated into the existing production line.